So for some of you this might seem really basic, but I love to share new things that I have tried in hopes in giving someone else the courage to try it. I tend to stay inside the box and not venture out too much, so this is one case where I actually did.
I was working in the studio creating a piece when I realized I didn’t have any more thick bezel stock wire that I just buy from Rio Grande. I like this particular wire because it is thicker and easier to work with then the thinner gauge bezel.
So I decided to try something that I have seen before. A little while back I purchased this cool tool I came across on Etsy from Horseshoe Engravers. The tool is called a Bezel Indexing Tool, in case you want to look it up. So I decided to give it a try.
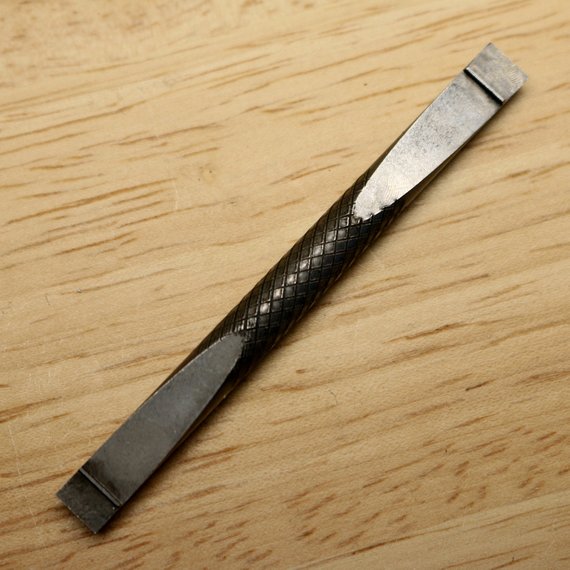
I took a sheet of 20g sterling silver and, using a pair of calipers, scribed a line based on the thickness of bezel wire I wanted (thickness meaning height). I used my jeweler saw to saw it out. Length is going to be dependent on the stone you use.
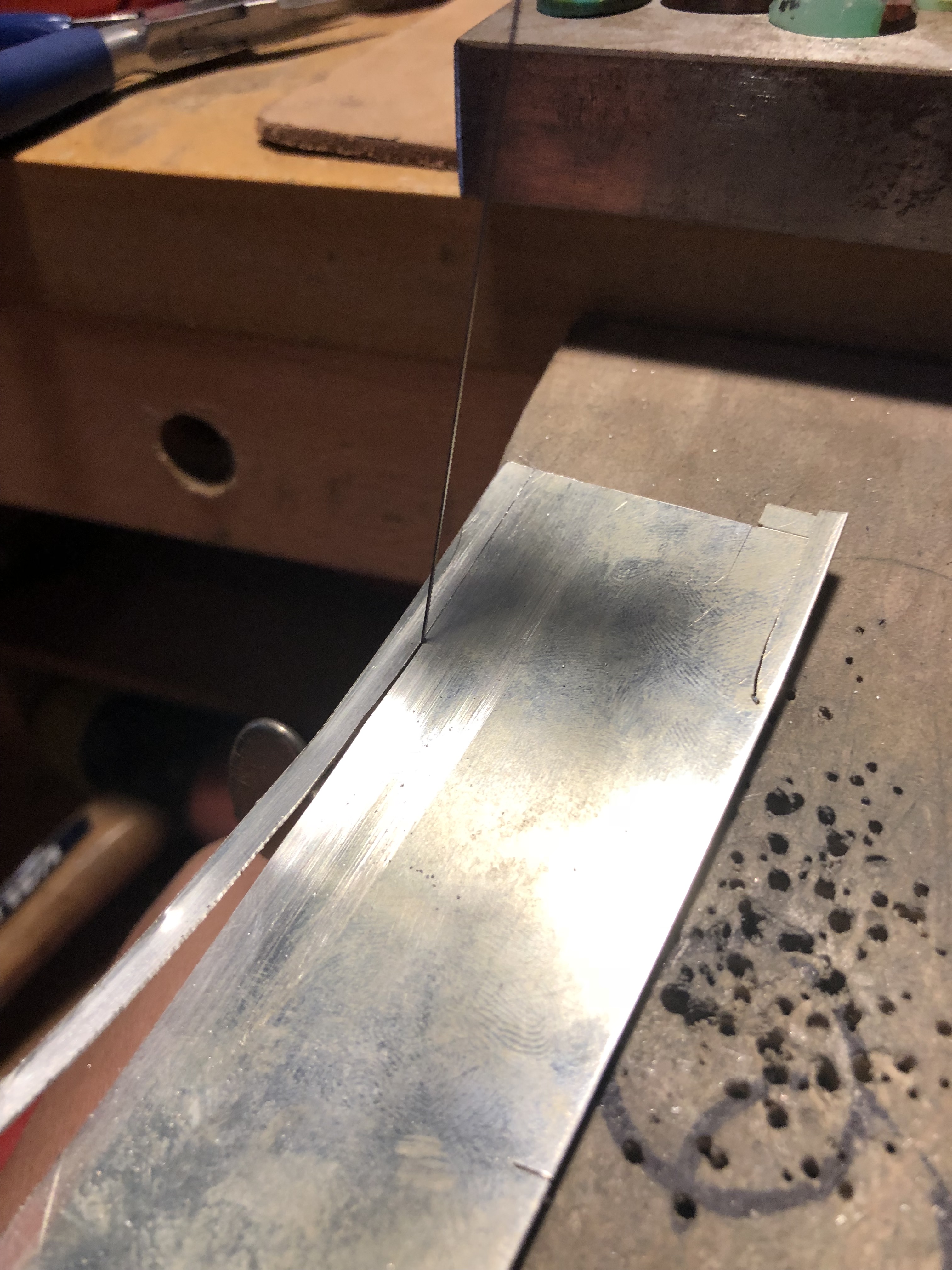
I then decided how deep I want the teeth on my bezel wire to be. Using masking tape I mask off where I want my saw marks to end, since I want them all to be even. I place this strip in the vise up to the mask line and now I will be able to maintain evenness in depth of my saw marks.
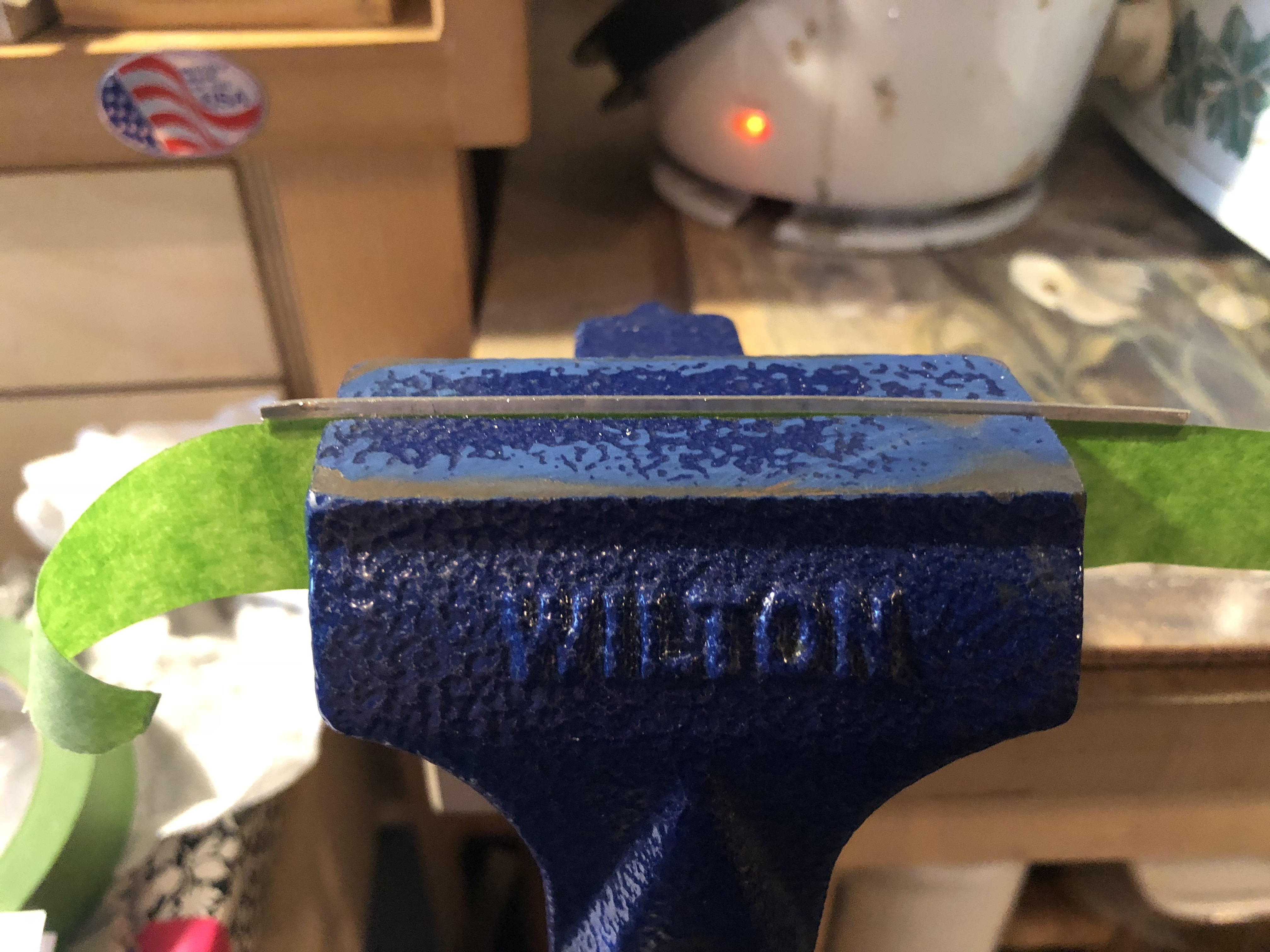
I make the first saw mark and then place the indexing tool in that first saw mark. I then make my second cut at the end of the tool. This tool creates a even space which is created by the spacing of the notch on the tool and the end of the indexer. I hope this makes sense, see image.
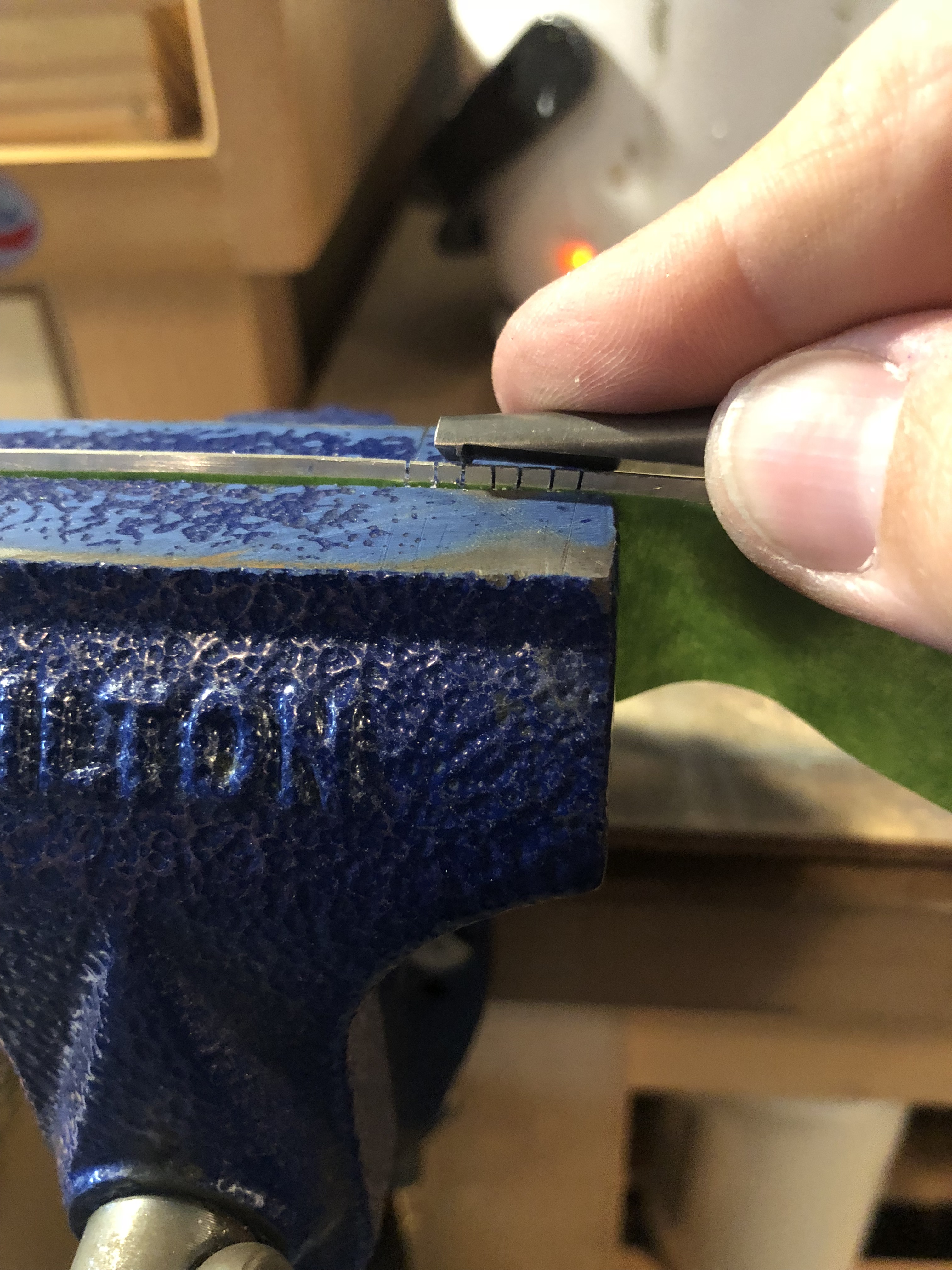
You keep moving along with the tool. Saw mark, place notch in the saw mark, create another saw mark at the end of the tool. Keep moving along the silver this way.
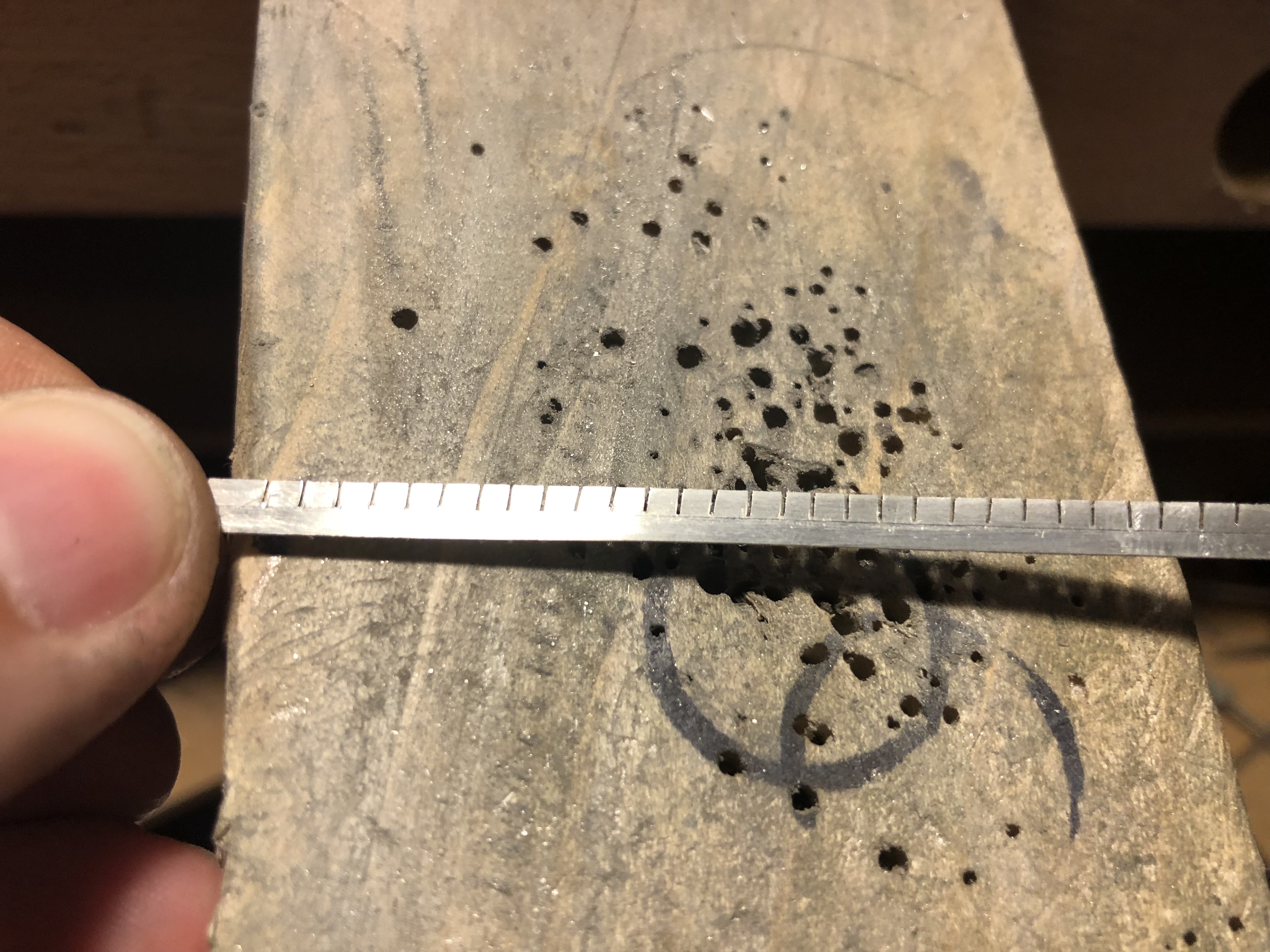
At this point I use a sanding disc on my dremel to make the saw lines more open and even. I haven’t quite mastered making the saw marks straight yet, but I was able to correct this with the sanding discs.
Then I continue on forming the bezel around the stone, soldering to a back, and soldering on a ring shank.
{“cameraType”:”Dual”,”macroEnabled”:false,”qualityMode”:2,”deviceTilt”:0.02205149730178313,”customExposureMode”:1,”extendedExposure”:false,”whiteBalanceProgram”:0,”cameraPosition”:1,”focusMode”:1}
{“cameraType”:”Dual”,”macroEnabled”:false,”qualityMode”:2,”deviceTilt”:0.11668340762587981,”customExposureMode”:1,”extendedExposure”:false,”whiteBalanceProgram”:0,”cameraPosition”:1,”focusMode”:1}
{“cameraType”:”Dual”,”macroEnabled”:false,”qualityMode”:2,”deviceTilt”:-0.013205459341406822,”customExposureMode”:1,”extendedExposure”:false,”whiteBalanceProgram”:0,”cameraPosition”:1,”focusMode”:1}
{“cameraType”:”Dual”,”macroEnabled”:false,”qualityMode”:2,”deviceTilt”:-0.031187329441308975,”customExposureMode”:1,”extendedExposure”:false,”whiteBalanceProgram”:0,”cameraPosition”:1,”focusMode”:1}
{“cameraType”:”Dual”,”macroEnabled”:false,”qualityMode”:2,”deviceTilt”:-0.023759957402944565,”customExposureMode”:1,”extendedExposure”:false,”whiteBalanceProgram”:0,”cameraPosition”:1,”focusMode”:1}
{“cameraType”:”Dual”,”macroEnabled”:false,”qualityMode”:2,”deviceTilt”:-0.011379341594874859,”customExposureMode”:1,”extendedExposure”:false,”whiteBalanceProgram”:0,”cameraPosition”:1,”focusMode”:1}
{“cameraType”:”Dual”,”macroEnabled”:false,”qualityMode”:2,”deviceTilt”:-0.0076954974792897701,”customExposureMode”:1,”extendedExposure”:false,”whiteBalanceProgram”:0,”cameraPosition”:1,”focusMode”:1}
{“cameraType”:”Dual”,”macroEnabled”:false,”qualityMode”:2,”deviceTilt”:0.12144820292922454,”customExposureMode”:1,”extendedExposure”:false,”whiteBalanceProgram”:0,”cameraPosition”:1,”focusMode”:1}
Not too shabby for my first time. I was pretty happy with the final product!